Yknow, I actually would really like to know how to stop this nonsense happening…
0.5mm tapered ballnose in maple, doing a raster finish pass in the grain direction, I keep getting these nests of strandy stuff on descending sloped sections, takes an annoying amount of cleanup to remove
Any ideas how to adjust the parameters to stop it? Tends to happen in oak as well
That is not a programming issue per se. That is material and setup. Wood is going to do that. It is fibrous, and will tend to tear like this instead of cut (especially if it isn’t 100% dry). There is also chatter that I can see, meaning the work needed to be more secure. One thing that I have learned with the few instances I have worked with wood is to seriously just max out the machine on feed and speed.
I’d don’t know your setup (or setup practices) but the tldr here is to hold the work tighter and let it rip. Wood is like butter to an end mill like that.
Oh yeah. Don’t use the tiny end mill for everything. Use maybe a 2mm ball nose as a roughing pass. Let the big one do the work, then go in for the details.
Your average woodworking router is already running at something like 20k RPM for ~6mm and larger bits. High speed should do fine on wood, at whatever feed rate doesn’t burn it. Maybe just use light passes to save your endmills.
That said, I am most assuredly NOT a CNC machinist, just a nerd with woodworking tools and a couple of low end maker devices that run gcode.
Yknow, I actually would really like to know how to stop this nonsense happening…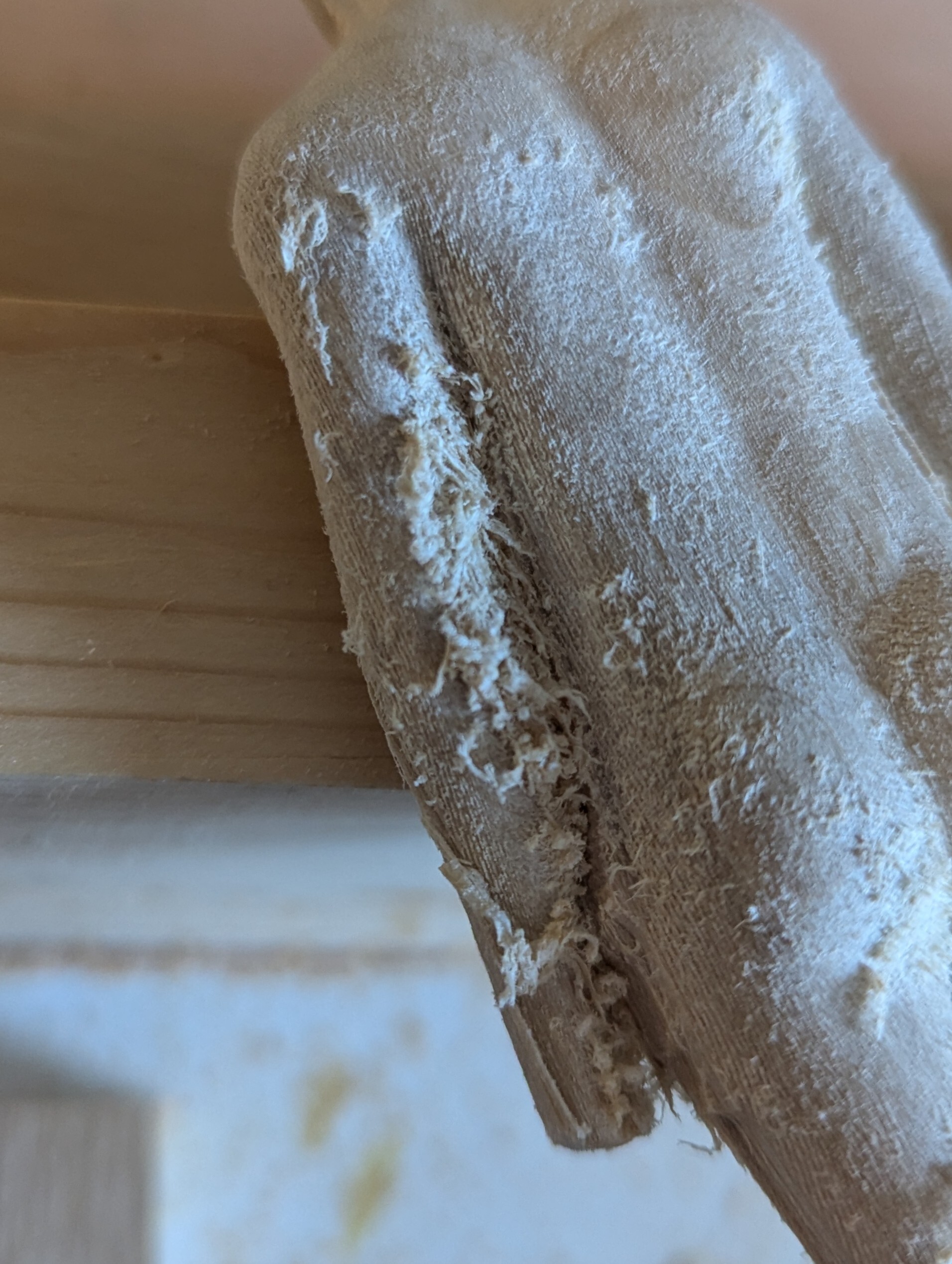
0.5mm tapered ballnose in maple, doing a raster finish pass in the grain direction, I keep getting these nests of strandy stuff on descending sloped sections, takes an annoying amount of cleanup to remove
Any ideas how to adjust the parameters to stop it? Tends to happen in oak as well
That is not a programming issue per se. That is material and setup. Wood is going to do that. It is fibrous, and will tend to tear like this instead of cut (especially if it isn’t 100% dry). There is also chatter that I can see, meaning the work needed to be more secure. One thing that I have learned with the few instances I have worked with wood is to seriously just max out the machine on feed and speed.
I’d don’t know your setup (or setup practices) but the tldr here is to hold the work tighter and let it rip. Wood is like butter to an end mill like that.
Thanks! Yeah I’m always a bit wary of running these bits too fast, I’ve broken far too many lately, but I’ll max out the rpm and see what happens 🤞
Oh yeah. Don’t use the tiny end mill for everything. Use maybe a 2mm ball nose as a roughing pass. Let the big one do the work, then go in for the details.
Your average woodworking router is already running at something like 20k RPM for ~6mm and larger bits. High speed should do fine on wood, at whatever feed rate doesn’t burn it. Maybe just use light passes to save your endmills.
That said, I am most assuredly NOT a CNC machinist, just a nerd with woodworking tools and a couple of low end maker devices that run gcode.